Thought this would be an interesting discussion. Hope it fuels a good discussion about building boats with plywood, resin, and fiberglass but not an outright raging fire.
As you may know, I demonstrated a technique to help with with panels alignment:
The spacers create a small gap between the panels so all the assembly pressure is on the spacers themselves and not the panel edges. This make it easier to control and keep aligned.
The gap that is created must be filled in. This is a good thing on larger craft that must withstand much greater forces and pressures than a paddle craft. On these boats built with modern methods (fiberglass and resin), hard contact between panels is not desired. The filling in these gaps can better distribute loads and dissipate sudden shocks evenly to the rest of the hull where as hard wood-on-wood contacts isolated shock pressures to a single, localized area and creates a greater risk of hull damage of failure. Kind of like the cartilage between you bones vs. bone-on-bone contact. Not quite the same but you get the idea.
But again, this is less important on small paddle craft since the loads and pressures are not as great.
There's a nice demonstration of this concept on a stitch and glue boat here:
http://www.bbkayak.com/kit.htm
They exaggerate things a bit in there "typical boat kit" picture as most designs call for interior hull seams to get fiberglass coverage and not just left bare. Most designs call for at least 4mm ply as well.
However, the bottom image shows a good example of how panel edges are captures and how you can get a more-rounded exterior seam. The draw back is that the density of filler in the seams is more than the density of plywood so it ads weight. Looks like they address it by using 3mm ply and 4-ounce s-glass.
So anyway, thought this might kick off an interesting discussion.

As you may know, I demonstrated a technique to help with with panels alignment:
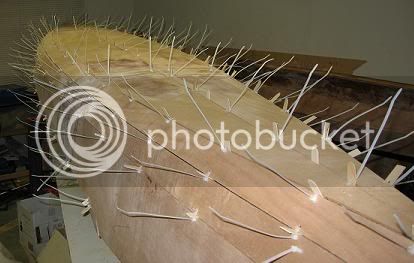
The spacers create a small gap between the panels so all the assembly pressure is on the spacers themselves and not the panel edges. This make it easier to control and keep aligned.
The gap that is created must be filled in. This is a good thing on larger craft that must withstand much greater forces and pressures than a paddle craft. On these boats built with modern methods (fiberglass and resin), hard contact between panels is not desired. The filling in these gaps can better distribute loads and dissipate sudden shocks evenly to the rest of the hull where as hard wood-on-wood contacts isolated shock pressures to a single, localized area and creates a greater risk of hull damage of failure. Kind of like the cartilage between you bones vs. bone-on-bone contact. Not quite the same but you get the idea.
But again, this is less important on small paddle craft since the loads and pressures are not as great.
There's a nice demonstration of this concept on a stitch and glue boat here:
http://www.bbkayak.com/kit.htm
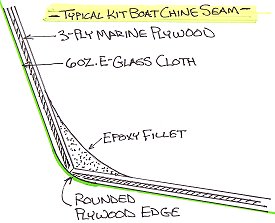
They exaggerate things a bit in there "typical boat kit" picture as most designs call for interior hull seams to get fiberglass coverage and not just left bare. Most designs call for at least 4mm ply as well.
However, the bottom image shows a good example of how panel edges are captures and how you can get a more-rounded exterior seam. The draw back is that the density of filler in the seams is more than the density of plywood so it ads weight. Looks like they address it by using 3mm ply and 4-ounce s-glass.
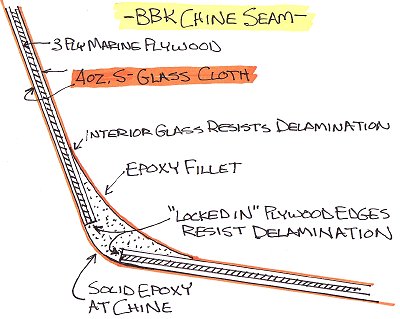
So anyway, thought this might kick off an interesting discussion.